Авторы: А.А. Алексеев, к.т.н., М.А. Алексеев, к.т.н., А.В. Балашов (ЗАО "ЭМИКОН")
В этом году ЗАО «ЭМИКОН» отмечает четверть века своей работы в отрасли производства средств и систем промышленной автоматизации.
Со дня своего образования основной концепцией фирмы стала разработка и производство микропроцессорных программируемых контроллеров, не уступающих по техническим характеристикам лучшим зарубежным аналогам.
За 25 лет работы фирма накопила серьезный опыт в области разработки и производства программируемых логических контроллеров (ПЛК), а также в создании систем автоматизации технологических процессов с использованием этих контроллеров в различных отраслях промышленности.
Первый контроллер серии ЭК-1000 на базе самого мощного в тот момент микропроцессора КР1810ВМ86 был создан в 1991 году исключительно на отечественной элементной базе. В нем были реализованы некоторые схемотехнические решения (например, троирование контактов разъемов системной шины), которые позволили достичь достаточно высоких надёжностных характеристик. Контроллер стал основой систем автоматизации, внедренных в ряде отраслей народного хозяйства: в коммунальных городских службах, на предприятиях аграрно-промышленного комплекса. С 1992 г. контроллеры ЭК-1000 начали поставляться предприятиям чёрной металлургии (АСУ прокатных станов, мартеновских цехов и др.).
В связи с развалом отечественной электронной промышленности и с появлением возможности использования импортных комплектующих изделий, начиная с 1993 года, практически все новые разработки велись на базе электронных компонентов ведущих мировых фирм. Так была создана серия ЭК-2000, которая нашла широкое применение во многих отраслях промышленности: в металлургии, в трубопроводном транспорте нефти, нефтепродуктов и газа, в атомной промышленности (на заводах по обогащению урана), в ракетно-космической и военной промышленности.
Модернизированные контроллеры этой серии и сейчас востребованы предприятиями вышеперечисленных отраслей.
В 1995 г. на базе контроллеров серии ЭК-2000 был разработан и изготовлен опытно-промышленный образец микропроцессорной системы автоматического регулирования давления с электроприводом (МСАРДЭ). Успешное внедрение МСАРДЭ на магистральных нефтепроводах ПНБ "Тихорецкая" (ОАО "Черномортранснефть") привело к тому, что в 1996 году фирма была приглашена к участию в конкурсе АК «Транснефть» на поставку системы автоматики НПС. Письмом от 31.10.1996 №18-15/3036 вице-президент АК «Транснефть» А.С. Джарджиманов сообщил: "Всестороннее рассмотрение нашими экспертами представленных АО «ЭМИКОН» и другими организациями технико-коммерческих предложений на поставку системы автоматики НПС, доработанных до эскизного проекта, показало, что, в сравнении с предложениями других участников конкурса, предложения АО «ЭМИКОН» - наиболее предпочтительны".
АК «Транснефть» предлагает АО «ЭМИКОН» продолжить начатую работу в рамках договора с АК «Транснефть» на разработку, изготовление и поставку опытного образца системы с приемочными испытаниями образца на действующей НПС.
СА НПС, разработанная нами, обеспечивала автономное поддержание режимов работы насосных агрегатов, задвижек, вспомогательных систем, а также изменение этих режимов либо автоматически, либо по командам с АРМа оператора-технолога как из местного диспетчерского пункта (МДП), так и из вышестоящего уровня управления - районного диспетчерского пункта (РДП). Микропроцессорная система автоматизации НПС "Родионовская-1" (АООТ ПМН, в настоящее время ОАО "Черномортранснефть") прошла приемочные испытания и была введена в эксплуатацию в 1998 г. С этого момента предприятия трубопроводного транспорта нефти и нефтепродуктов стали основными заказчиками для ЗАО «ЭМИКОН».
В 1999 году на базе модулей серии ЭК-2000 был разработан контроллер КСАП, предназначенный для использования в системах управления автоматическим пожаротушением. Контроллер одним из первых в стране был сертифицирован как микропроцессорный пожарный прибор приемно-контрольный и управления. Это позволило строить многофункциональные автономные системы автоматического пожаротушения, как для объектов нефтегазовой отрасли, так и других пожароопасных промышленных объектов. На контроллер был получен сертификат пожарной безопасности ГПС МВД России. Программно-технические комплексы систем автоматического пожаротушения (ПТК САП), выполненные на базе этих контроллеров, начали широко применяться в нефтегазовой отрасли (в системах автоматического пожаротушения нефтеперекачивающих станций, резервуарных парков, нефтебаз, объектов нефте- и газодобычи).
В последующие годы были разработаны еще несколько серий модулей, используемых в контроллерах для систем автоматизации.
С 2001 года ЗАО «ЭМИКОН» начинает серийно выпускать контроллеры серии DCS-2000, имеющие резервированную сетевую структуру и предназначенные для построения распределённых систем управления, и активно применять их в новых разработках АСУ ТП для трубопроводного транспорта нефти и нефтепродуктов. |
|
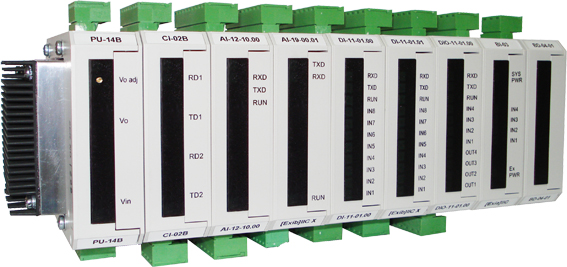 |
Учитывая высокую надежность контроллеров этой серии, предприятия атомной энергетики стали использовать их как базовые устройства для создания микропроцессорных систем автоматизации основных производств.
Для автоматизации небольших объектов, а также для создания распределенных систем управления в 2003 году были разработаны малоканальные контроллеры серии DCS-2001, которые нашли своё применение в металлургической промышленности (в частности, на Оскольском электрометаллургическом комбинате для линии непрерывной разливки стали).
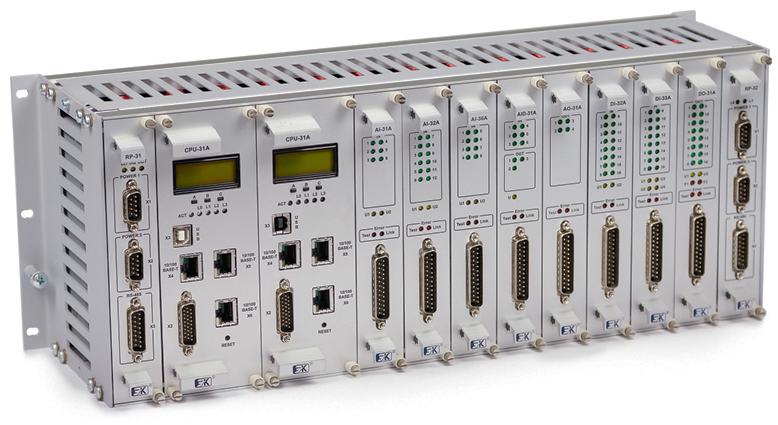
|
|
В 2010 году линейка выпускаемых контроллеров была расширена за счет модулей серии DCS-2000 каркасного исполнения, отличающихся повышенной производительностью и надежностью.
В настоящее время модули этой серии широко используются при построении СА нефтеперекачивающих станций магистральных нефтепроводов и практически во всех новых разработках систем автоматизации, осуществляемых ЗАО «ЭМИКОН». |
Программирование всех контроллеров ЭМИКОН осуществляется в среде "Cont Designer", разработанной ЗАО «ЭМИКОН» и включающей в себя также конфигураторы модулей удаленной связи с объектом и информационных каналов контроллера.
Основной принцип работы ЗАО «ЭМИКОН» - комплексность, охватывающая все этапы поставки АСУ ТП, начиная с участия в открытых конкурсах по выбору поставщиков и заканчивая сдачей объекта в эксплуатацию. Предпроектное обследование объекта автоматизации, проектирование, комплексирование, производство, поставка, организация строительно-монтажных работ, обучение обслуживающего персонала, пуско-наладка и сдача в эксплуатацию – оперативное осуществление всех перечисленных этапов позволяет значительно сокращать сроки ввода в эксплуатацию объектов и затраты на реализацию проектов. Важным аспектом также является гарантийное и сервисное пожизненное обслуживание введенных в эксплуатацию систем автоматизации.
По количеству внедрённых микропроцессорных систем автоматизации нефтеперекачивающих станций, резервуарных парков и нефтебаз для нефтегазовой отрасли фирма «ЭМИКОН» сохраняет в настоящее время лидирующее положение. За период с 1995 г. по 2012 г. было внедрено: 82 системы автоматизации нефтеперекачивающих станций (НПС), резервуарных парков (РП) и нефтебаз (НБ), 113 систем автоматического пожаротушения и 27 систем автоматического регулирования давления (САРД).
Всего же за 25 лет работы ЗАО «ЭМИКОН» на базе наших контроллеров в различных отраслях промышленности России было создано более 700 систем автоматизации технологических процессов и систем автоматического пожаротушения.
Поставляемые ЗАО «ЭМИКОН» системы автоматизации могут выполняться в различных вариантах. По требованию заказчика в качестве центрального контроллера СА, в наших разработках часто используются процессорные модули MODICON фирмы «Schneider Electric» и др. При этом контроллеры ЭМИКОН интегрируются в данные системы в качестве контроллеров удаленного ввода/вывода. В составе контроллеров реализуются дополнительные функциональные блоки, такие как встроенные барьеры искробезопасности, блоки питания датчиков и др. В зависимости от конкретной задачи контроллеры ввода/вывода реализуют как простейшие алгоритмы нормализации и фильтрации входных сигналов, так и алгоритмы локальных систем (САРД, КАЗ и др.). Это позволяет создавать более гибкие и максимально адаптированные под поставленные задачи системы.
Примером реализации такой структуры может служить микропроцессорная система автоматизации (МПСА) нефтеналивного терминала (ННТ) «Усть-Луга», конечной точки «Балтийской трубопроводной системы - 2» (ОАО «АК «Транснефть»), которая была создана в соответствии с техническим заданием на поставку, разработанным ОАО «Гипротрубопровод». Проектирование было выполнено на основе накопленного многолетнего опыта ОАО «АК «Транснефть» в области автоматизации объектов магистральных нефтепроводов, отраженном в руководящем документе АК «Транснефть» «Автоматизация и телемеханизация магистральных нефтепроводов. Основные положения» (РД-35.240.00-КТН-207-08) и в документе «Комплекс типовых проектных решений автоматизации НПС и резервуарных парков на базе современных типовых решений и комплектующих» (ТПР-35.240.10-КТН-012-10).
Система предназначена для обеспечения автоматизации технологических процессов приема нефти из магистрального нефтепровода в резервуарный парк, подачи нефти из резервуарного парка к причальным сооружениям, налива нефти в танкеры, внутрибазовых перекачек, контроля и защиты основного и вспомогательного технологического оборудования и сооружений ННТ. МПСА обеспечивает автономное поддержание заданных режимов работы наливной насосной станции, причальных сооружений, оборудования нефтебазы (НБ) и управление им по командам с автоматизированных рабочих мест (АРМ) диспетчера нефтебазы, локальных АРМ, по каналам телемеханики из районного диспетчерского пункта (РДП).
МПСА включает в себя пять взаимосвязанных подсистем:
- систему автоматизации (СА) нефтебазы;
- СА наливной насосной станции №1;
- СА наливной насосной станции №2;
- СА причалов и береговых сооружений;
- СА канализации и очистных сооружений.
СА нефтебазы «Усть-Луга» выполняет контроль, управление резервуарным парком, системой откачки утечек, приточной и вытяжной вентиляцией насосной станции, котельной, водоснабжением, энергоснабжением и другими системами.
СА наливных насосных станций выполняют контроль, управление и защиту наливных насосных станций, управление, контроль и защиту насосных агрегатов (8 шт.).
СА причалов и береговых сооружений предназначена для обеспечения контроля параметров, управления, сигнализации и автоматической защиты объектов причальных сооружений.
СА канализации и очистных сооружений выполняет контроль и управление оборудованием производственно-дождевой канализации и хозяйственно-бытовой канализации.
Безопасная совместная работа всех СА реализована за счет отработки аварийных защит всеми системами одновременно, что возможно благодаря организации интерфейсной связи между ними по сети Ehternet (протокол Modbus TCP).
Кроме того, МПСА связана с другими локальными автоматизированными системами НБ: системой измерения количества и показателей качества нефти (СИКН), системой измерения уровня в резервуарах (СИУ), системой автоматического пожаротушения (САП), автоматизированной системой технического учета электроэнергии (АСТУЭ).
МПСА имеет трехуровневую структуру.
Нижний уровень включает в себя датчики и вторичные преобразователи, обеспечивающие формирование входных электрических аналоговых и дискретных сигналов системы автоматизации, и показывающие приборы, устанавливаемые по месту на приборных шкафах, щитах (стойках) или непосредственно на технологическом оборудовании, а также органы управления, входящие в состав технологических объектов управления. В системе применяются приборы лучших зарубежных и отечественных производителей, имеющих большой опыт применения и хорошо зарекомендовавших себя на объектах магистрального транспорта нефти. Задвижки, применяемые в системе, имеют интеллектуальные приводы.
Средний уровень включает в себя программируемые логические контроллеры:
- СА НБ: контроллер центральный (КЦ НБ) и контроллеры связи с объектом (УСО1 – УСО3, УСО8 – УСО15);
- СА наливной насосной станции: контроллеры центральные: (КЦ ННС-1, КЦ ННС-2) и контроллеры УСО (УСО4 – УСО7);
- СА канализации и очистных сооружений: контроллер центральный ЦПУ К и контроллер УСО К;
- СА причалов и береговых сооружений: контроллер центральный и контроллеры УСО1.1, УСО1.2, УСО2.1, УСО2.2, УСО2.3, УСО3.1.
Контроллеры центральные МПСА выполнены по схеме «горячего» резервирования и реализованы на базе модулей Modicon Quantum фирмы "Schneider Electric". Контроллеры УСО выполнены на базе модулей серии DCS-2000 фирмы «ЭМИКОН». Такой состав контроллеров обеспечивает выполнение нормативных требований к МПСА и ее типовую структуру, заложенную в проекте, с приемлемой стоимостью. В системе предусмотрена связь по интерфейсу (протокол Modbus RTU) с интеллектуальными устройствами: задвижками и заслонками с интеллектуальными приводами, устройствами размыва донных отложений, вентиляционными системами, устройствами контроля загазованности, станциями управления стендерами, системой управления швартовыми гаками, системой контроля вибрации. Волоконно-оптическая сеть связи среднего уровня выполнена по топологии самовосстанавливающегося дублированного кольца.
Верхний уровень включает в себя оборудование серверов, автоматизированные рабочие места операторов: АРМ местного диспетчерского пункта (МДП) (основной и резервный), АРМ НБ, АРМ наливной насосной ННС-1 и ННС-2, АРМ комплекса причальных сооружений, АРМ инженера-электроника и мониторинга, АРМ линейной телемеханики, АРМ контроля нормативных параметров, телекоммуникационное оборудование.
Верхний уровень обеспечивает:
- прием и отображение информации со среднего уровня;
- мониторинг и оперативное управление технологическим процессом;
- архивацию событий нижнего уровня и действий оператора;
- обмен данными с локальными системами автоматизации;
- связь с районным диспетчерским пунктом (РДП) по телемеханическому протоколу через порт Ethernet сервера ввода-вывода для осуществления управления под руководством РДП.
Связь с РДП в системе осуществляется также посредством телекоммуникационного контроллера, подключенного к КЦ НБ по протоколу Modbus TCP. Для решения задач удобства управления, надежности и ремонтопригодности верхний уровень МПСА реализован по схеме двойного резервирования с использованием общего для всей МПСА отказоустойчивого сервера ввода-вывода, подключенного по протоколу Modbus TCP ко всем КЦ СА, и локальными АРМ для каждой СА, подключенными по независимым линиям связи к своим КЦ. Для отображения всех технологических площадок НБ на верхнем уровне используется видеостена коллективного пользования. |
|
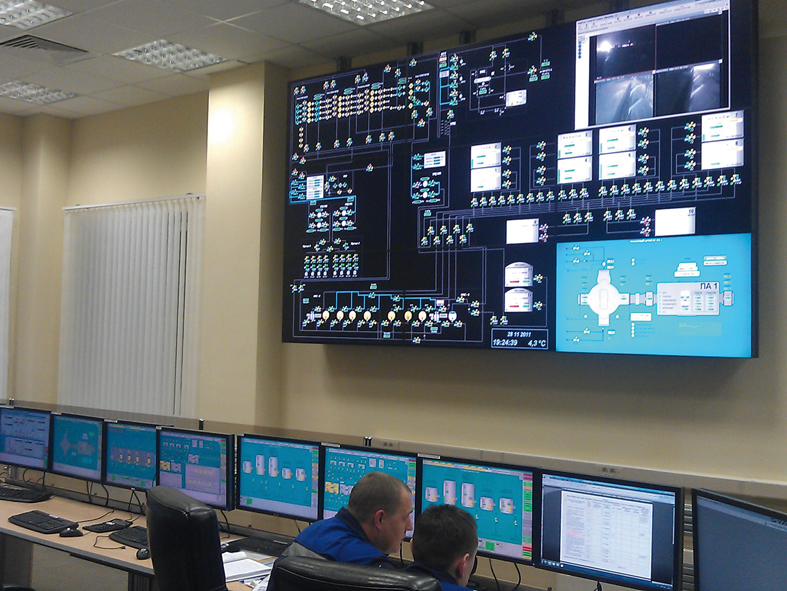 |
Основной и резервный АРМ МДП, АРМ инженера и контроллер видеостены с установленным клиентским программным обеспечением SCADA-системы iFix версии 5.0, получают данные для отображения и передают команды управления серверной части iFix, установленной на сервере ввода-вывода. В состав программного обеспечения (ПО) сервера ввода-вывода отказоустойчивой архитектуры входит сервер iFix, сервер журнала архива событий, СУБД, драйвер телемеханического протокола для обмена данными с РДП.
Для расчета параметров резервуарного парка на сервере ввода-вывода и на локальном АРМ НБ установлено программное обеспечение собственной разработки. Данное ПО на основе исходных данных, получаемых от КЦ СА НБ и АРМ SAAB Tank Radar, производит расчет всех объемно-массовых характеристик резервуаров. К таким характеристикам относятся: скорость изменения уровня нефти; аварийные, допустимые и нормативные уровни нефти; емкость в эксплуатации; общее наличие нефти; товарное наличие нефти; свободная емкость; технологический остаток; наличие подтоварной воды; тип, плотность и температура нефти; содержание соли и серы; и т.д. Полученные в процессе расчетов данные могут быть отображены: в общих таблицах, обобщенно - на кадрах резервуарного парка или подробно - на мнемосхеме отдельно выбранного для просмотра резервуара. Предусмотрена передача данных в РДП для последующей обработки и отображения.
Прикладное программное обеспечение АРМ оператора, разработанное на основе SCADA-пакета iFix, реализует отображение информации на экранах мониторов компьютеров (видеокадры, табличные формы, графики) для выполнения технологического мониторинга, формирование трендов по измеряемым параметрам, формирование архивной информации, файлов журнала событий и системного журнала, формирование команд управления с пульта оператора.
Дополнительной возможностью управления оборудованием является система автоматического построения и контроля маршрутов, реализованная на АРМ МДП и АРМ НБ.
Функционирование МПСА осуществляется в режиме реального времени, круглосуточно и непрерывно. Для синхронизации внутренних часов всего оборудования системы управления используется резервированный сервер точного времени, получающий сигналы от приемника GPS/ГЛОНАСС.
В СА нефтебазы реализована возможность управления задвижками СИКН по интерфейсной связи с ними (Modbus RTU) или посредством связи по Modbus TCP с контроллерами СИКН. Также реализована возможность задания параметров для работы систем регулирования давления СИКН (расход, давление).
Для программирования контроллеров КЦ используется интегрированная система программирования "Unity" фирмы "Schneider Electric".
Контроллеры УСО, построенные на базе модулей серии DCS-2000, программируются в среде «Cont Designer».
Технические решения, заложенные в МПСА ННТ «Усть-Луга» при ее проектировании и разработке, обеспечивают выполнение всех требований ОАО «АК «Транснефть» по контролю и управлению технологическими процессами, а также необходимую надежность и безопасность.
МПСА нефтебазы им. Хмура в г. Электроугли полностью выполнена на базе контроллеров ЭМИКОН серии DCS-2000.
Объект контроля и управления включает в себя:
- десять центробежных насосных агрегатов серии 3-АНГК (Н2…Н11);
- один центробежный насос серии 3-АНГК (Н1) для внутрибазовой перекачки всех видов топлива;
- 98 электроприводных задвижек;
- 65 ручных задвижек на железнодорожной эстакаде с концевыми выключателями контроля состояния (открыта-закрыта);
- девять резервуаров вертикальных с датчиками контроля уровня;
- помещения и оборудование нефтебазы (НБ), подлежащие контролю загазованности.
Микропроцессорная система автоматизации (МПСА) нефтебазы включает в себя:
- оборудование нижнего (полевого) уровня;
- центральный контроллер, реализующий алгоритмы работы МПСА, а также функции аварийных защит (пожар, аварийная загазованность, аварийный уровень в резервуарах, затопление насосной), и шесть контроллеров УСО;
- АРМ оператора НБ на основе компьютера с 2 мониторами 24'' и 50''.
Программное обеспечение верхнего уровня разработано в SCADA-пакете iFix 4,5.
МПСА связана с системой измерения уровня в резервуарах по OPC-интерфейсу.
Особенностью этой МПСА является то, что кроме контроля аварийных ситуаций, дистанционного и местного управления задвижками и насосами, дистанционного контроля процессов перекачки и слива топлива, система позволяет решать задачи интерактивного выбора маршрутов слива топлива из железнодорожных цистерн в резервуары хранения и маршрутов внутрибазовой перекачки, а также автоматического контроля готовности маршрутов.
Маршрут формируется на основе следующих исходных данных, вводимых оператором: вид топлива, номер резервуара-приемника, номер(номера) узла слива нефтепродукта (УСН), суммарный объем нефтепродукта и подтверждением множества предлагаемых системой насосов.
При внутрибазовой перекачке маршрут формируется заданием оператором номера резервуара-источника, номера резервуара-приемника и подтверждением множества предлагаемых системой насосов.
Формирование маршрута слива железнодорожных цистерн выполняется в соответствии со следующими этапами:
- проверкой соответствия свободного объема заданного резервуара-приемника заданному объему сливаемого продукта;
- автоматическим выбором насоса(насосов) из числа насосов, предназначенных для заданного вида топлива и не имеющих запрета на запуск по контролируемым параметрам агрегата. Количество насосов известной производительности определяется количеством одновременно подключаемых УСН и временными нормами слива;
- автоматическим выбором и открытием задвижек, относящихся к выбранному виду топлива, выбранным насосам (кроме задвижек на выходе агрегата) и выбранному резервуару;
- автоматическим контролем закрытого состояния задвижек, не относящихся к выбранному маршруту (выставляется запрет на открытие).
Формирование маршрута межрезервуарной перекачки выполняется в соответствии со следующими этапами:
- проверкой соответствия свободного объема заданного резервуара-приемника заданному объему перекачиваемого продукта;
- автоматическим выбором и открытием задвижек, относящихся к выбранному виду топлива, выбранным насосам (кроме задвижек на выходе агрегата) и выбранным резервуарам;
- автоматическим контролем закрытого состояния задвижек, не относящихся к выбранному маршруту (выставляется запрет на открытие).
При обнаружении невыполнимости формирования требуемого маршрута оператору выдаются сообщения с указанием причины (недостаточность свободного объема в резервуаре-приемнике, недостаточное количество насосов из-за их неготовности по определенному параметру, невыполнение открытия выбранных для маршрута задвижек и др.). На основании этих сообщений оператор корректирует задание на построение маршрута.
Реализована возможность распараллеливания технологических операций транспортировки нефтепродуктов при условии отсутствия конфликтов по разделяемому ресурсу – технологическому оборудованию.
После окончания формирования маршрута (маршрутов) выполняется автоматический контроль маршрута, заключающийся в автоматической проверке системой состояния задвижек и насосных агрегатов (НА). Если все контролируемые состояния и параметры в норме, подается команда на запуск НА. После запуска НА и до окончания слива выполняется текущий контроль состояния задвижек и насосных агрегатов. Если отклонения от нормы являются недопустимыми, выполняется защитное отключение НА и закрытие соответствующих задвижек, выдается соответствующее сообщение оператору.
Для удобства работы оператора в интерактивном режиме на видеокадре цветом, соответствующим заданному виду топлива, реализовано выделение технологического оборудования, относящегося к выбранному маршруту.
Также, в системе реализована возможность переназначения задвижек на маршруте, что обеспечивает большую гибкость в дальнейшей эксплуатации системы автоматики нефтебазы. Привязка задвижек производится до формирования маршрутов перекачки нефтепродукта и неизменна на протяжении операции.
В заключение хочется отметить, что 25 лет – это возраст зрелости, расцвета творческих и производственных сил.
Мы состоялись, мы справились и уверенно смотрим в будущее!